Why the drum does not spin in the washing machine
The drum of the washing machine can break down at any time, including during the washing process. This is an unpleasant, but not a critical situation, and in some cases the problem can be fixed on your own.
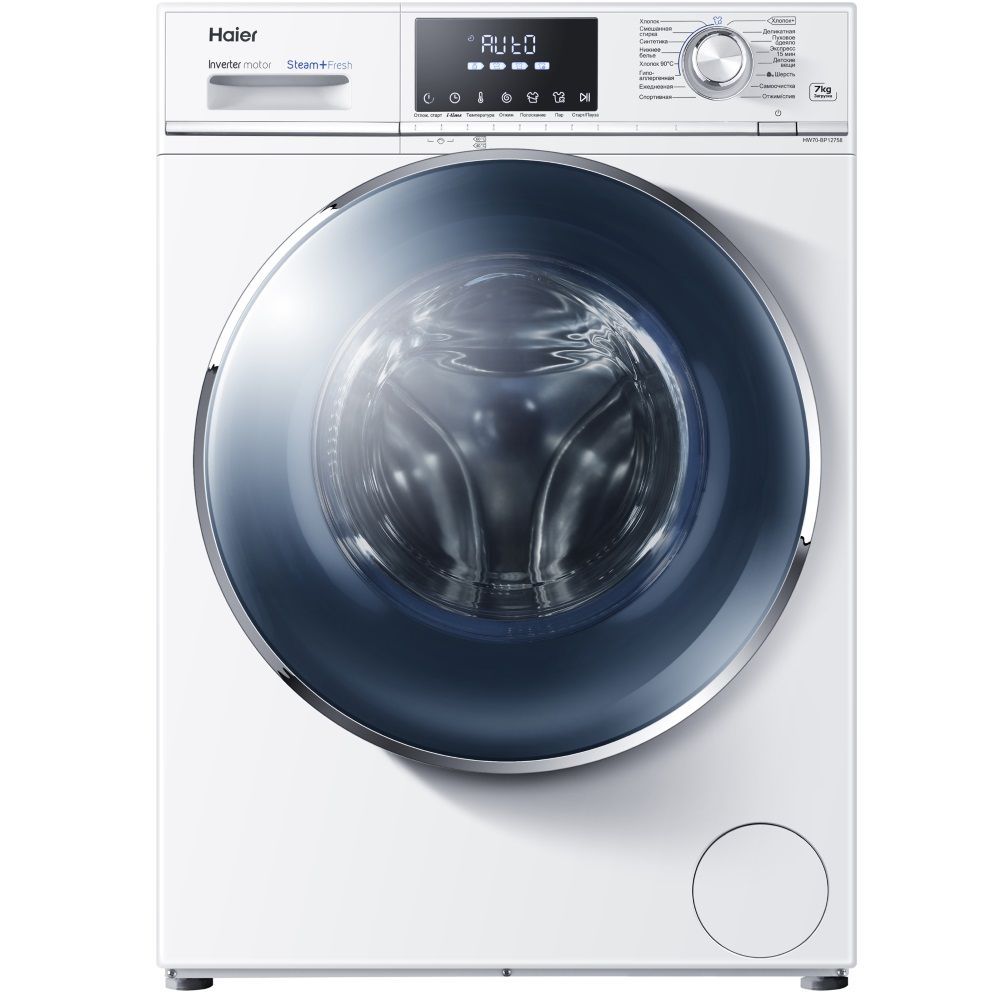
Why the washing machine does not turn the drum
If the drum stops rotating during the washing process, then first turn off the machine with the power button and unplug the cord, drain the water using the drain filter located on the lower front panel, and remove the laundry.
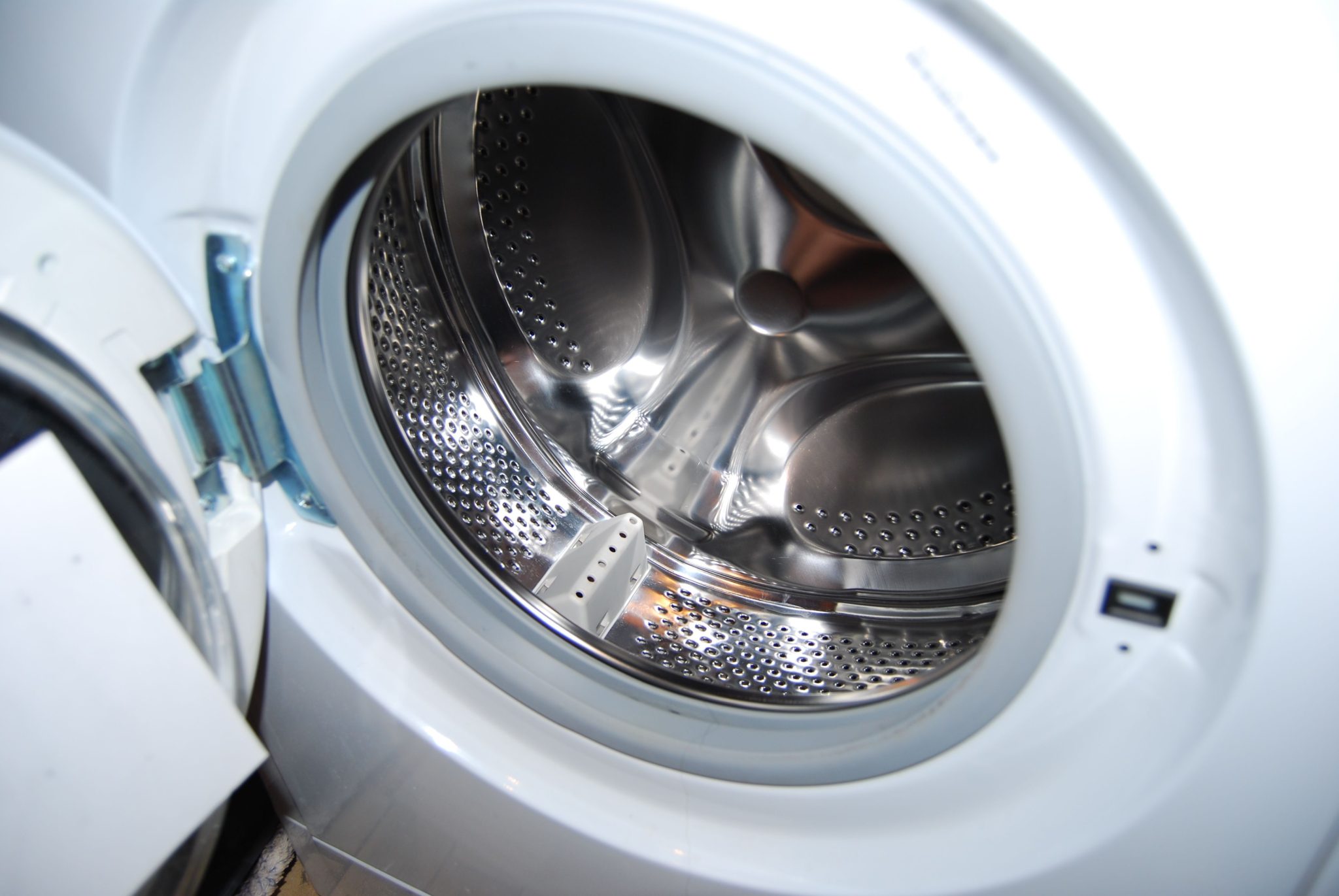
Note! To unscrew the drain filter plug, turn it clockwise. If it is impossible to pull it out by hand, it is permissible to use pliers.
Next, you need to determine at what point the drum stopped:
- When spinning. Can be determined by the condition of the laundry. If it is raw, but not soapy, then the problem is spinning.
- Is stuck in the wash. In this case, things will be soapy. If the drum of the washing machine does not rotate by hand, then it is physically prevented from doing it either by a foreign body.
- Rotates manually, but does not spin independently. In this case, the problem is faulty electronics.
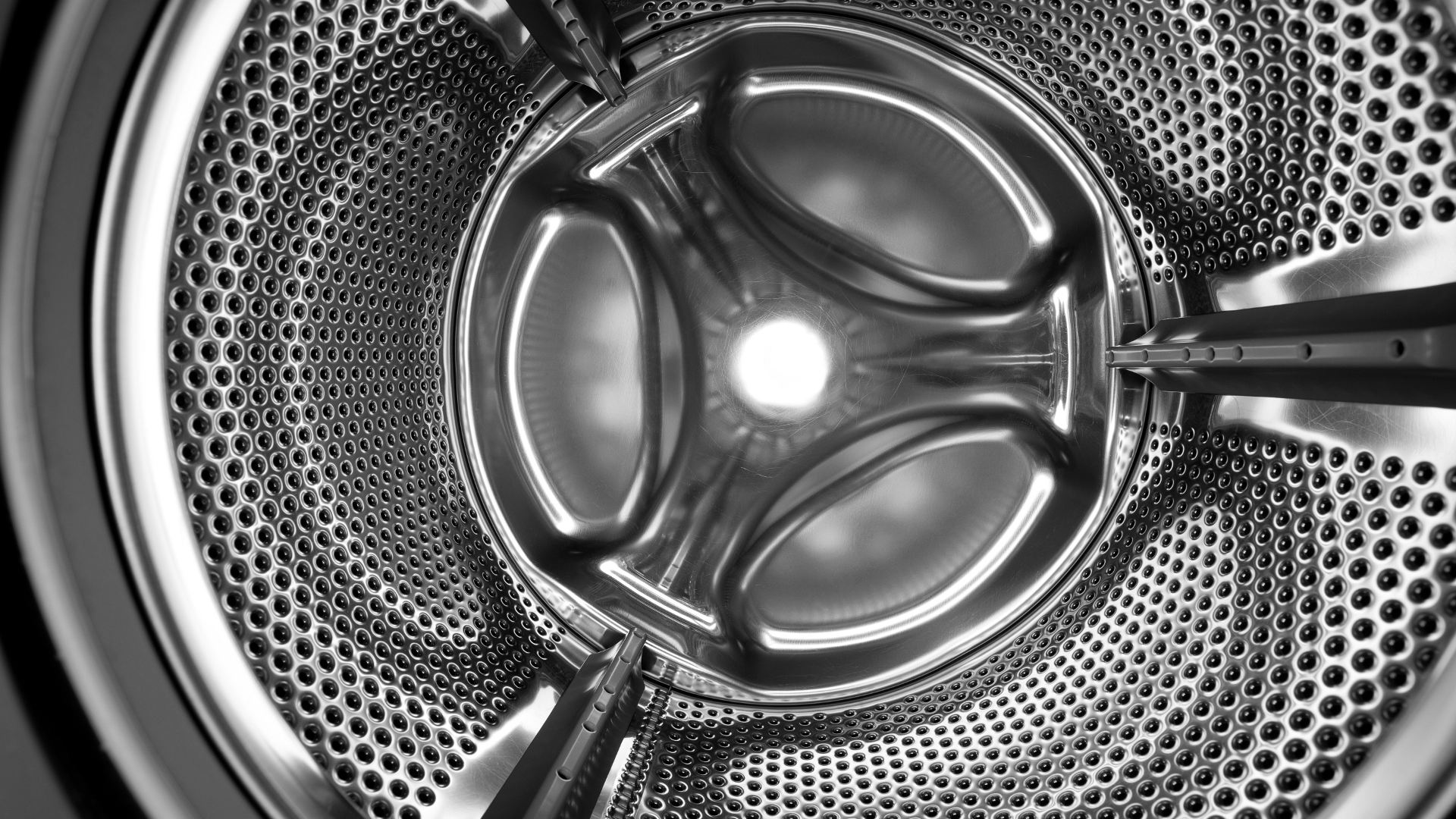
All car breakdowns can be divided into typical and rare. The drum stop belongs to the first group. This malfunction can be caused by technical, mechanical or domestic problems.
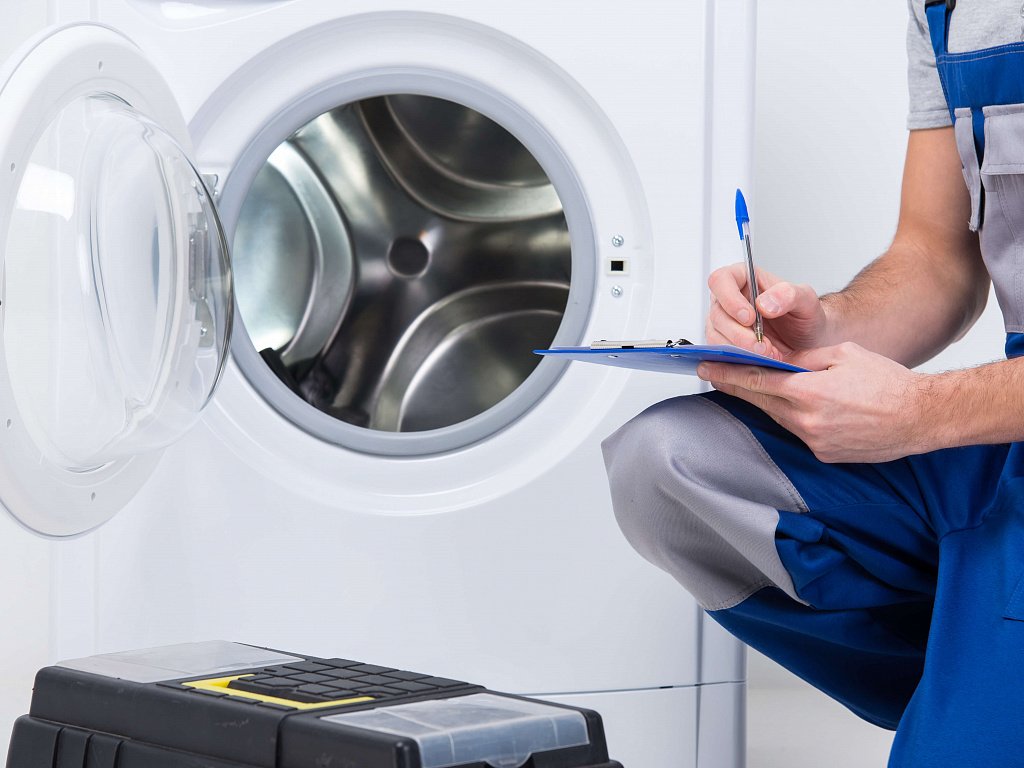
If the machine has been used for a long time without preventive maintenance, working at the limit of its capabilities, then technical breakdowns appear. To eliminate them, you need to invite a specialist. The rest of the problem can be dealt with on your own.
Critical weight
Drum immobility is often caused by simple overloading. To check that the cause of the malfunction is this, you need to divide the laundry into two parts and try to start the wash. Modern machines are equipped with sensors that monitor weight, and when overloaded, they simply slow down the process.
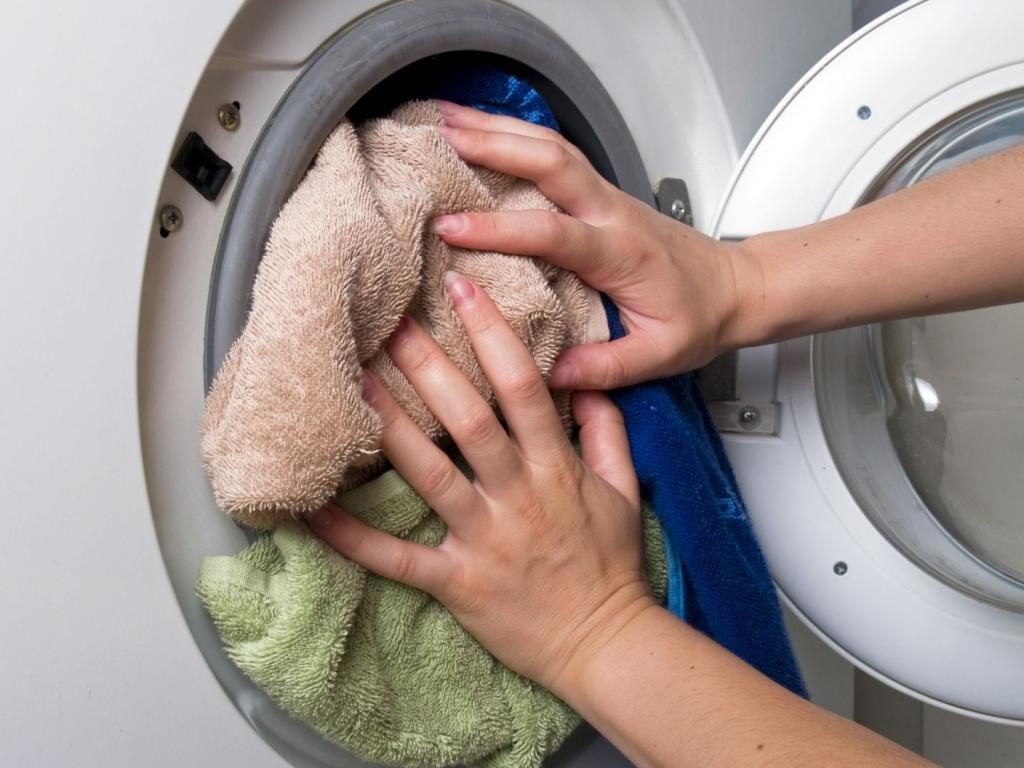
In some models, this information is displayed on the screen. If after such a reboot the machine works, then there is no breakdown. In the future, follow the instructions for downloading. If the manipulation did not help, then one of the nodes failed.
Foreign object in the tank
First, you need to carefully examine the inside of the drum. It is better to do this with a flashlight.
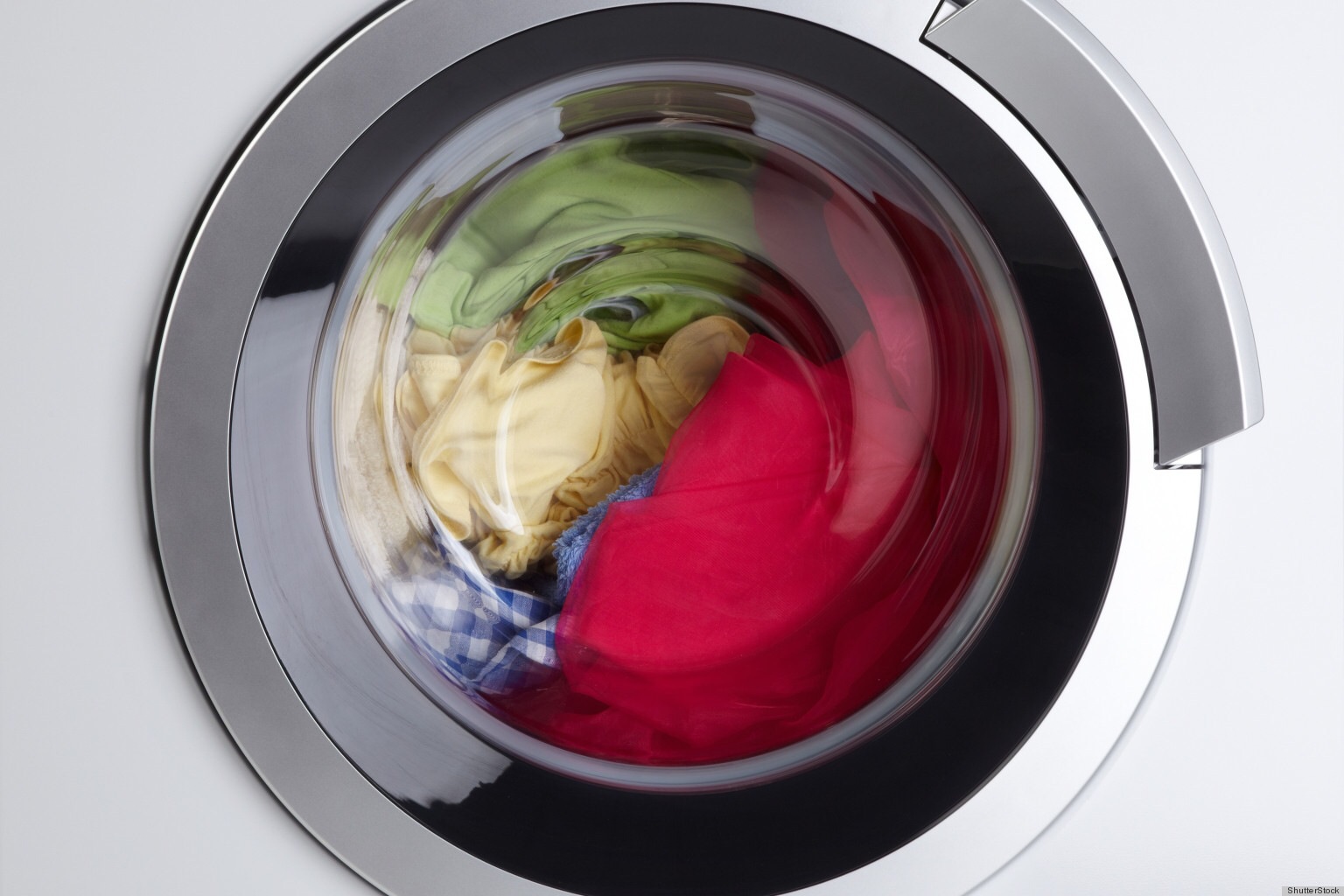
If a foreign object is found, the following actions are taken to remove it:
- Pull out the typewriter. This will provide access to it from all sides.
- Remove the screws on the rear wall holding the top cover.
- Remove the wall by sliding it back.
- Remove the rear cover by unscrewing the corresponding screws.
- Remove the heating element (TEN) to facilitate the process of reaching for foreign objects. For easier removal, you can pry it off with a screwdriver.
- Disconnect the wires going to the heating element and unscrew the fastening nut.
- Shine a flashlight into the resulting hole. Remove the detected foreign element with a suitable length of twisted wire.
- Reinstall the heating element and tighten all nuts. It is necessary to control the stocking density.
- Assemble the machine and put it in place.
Note! If the jammed object is above the drum, it cannot be seen through the hole. In this case, it is worth scrolling the drum manually so that the item goes down.
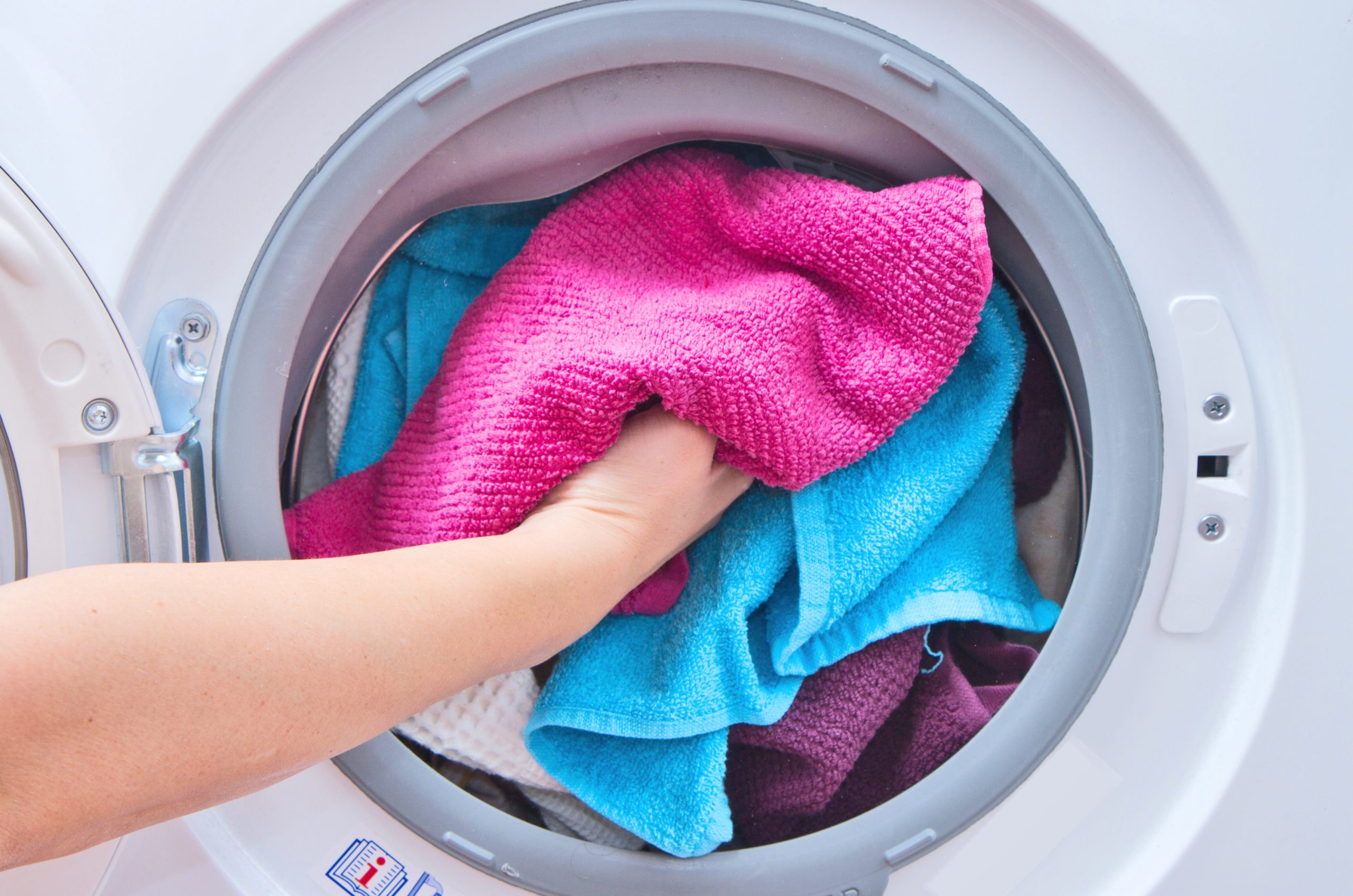
The doors opened vertically
In vertical machines, the tank flaps may open during the spinning process. This can be due to both a broken latch and a human factor. For example, a child could turn the drum with the flaps open, or an adult loaded too much laundry, which caused a piece of fabric to fall on the retainer.
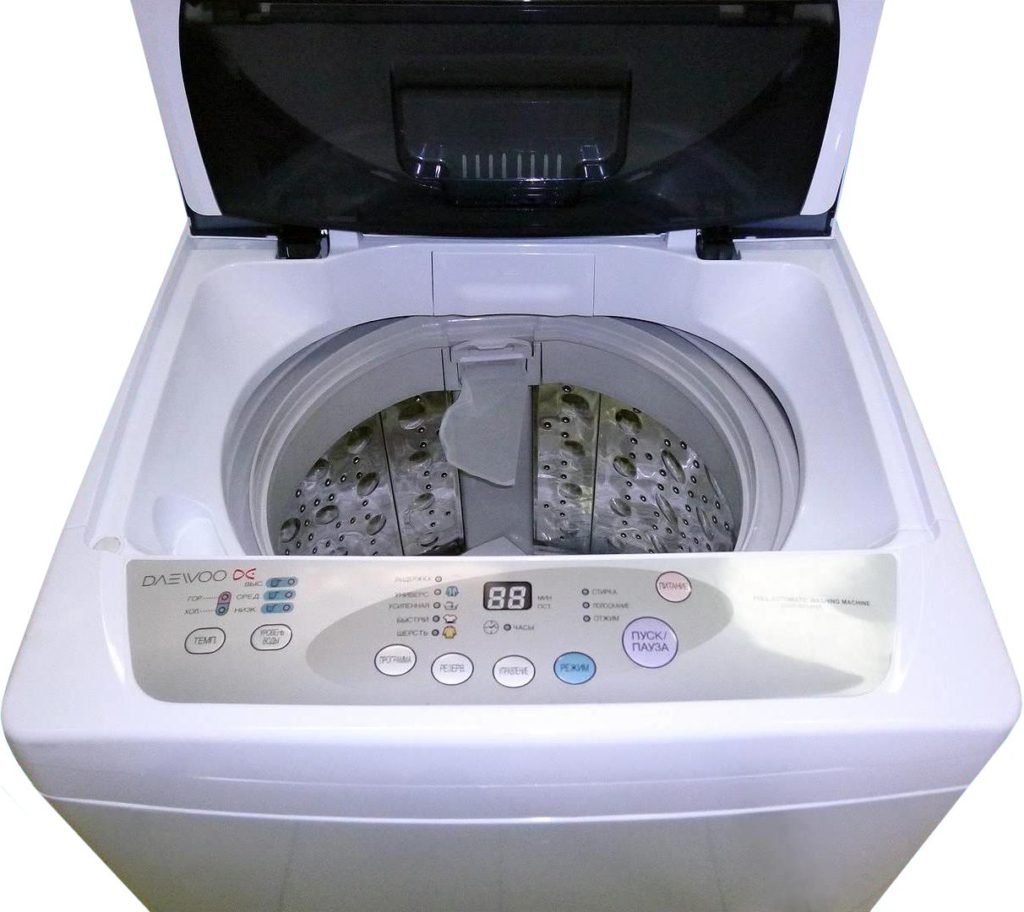
The metal doors themselves are closed with a sufficiently strong latch, but over time it wears out and looses, which leads to the opening. The consequences differ depending on the washing mode. With a delicate or gentle wash, nothing terrible happens. In the case of a strong spin, the blades are transformed into meat grinder knives, mercilessly destroying the loaded laundry.
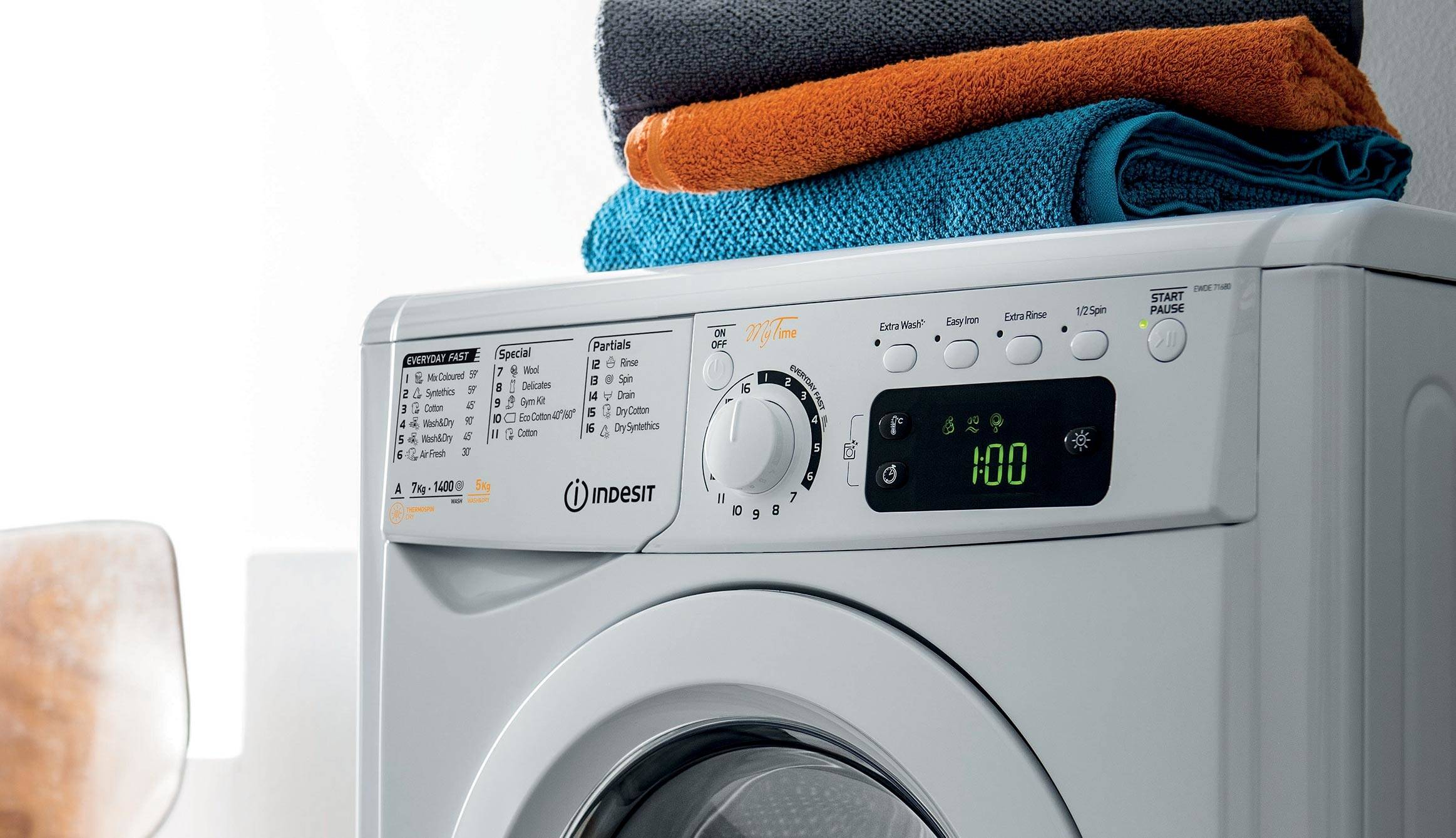
At speed, the open doors break through the protective barrier. This will damage the heating element, tank walls and drum flaps. If all these elements break down, it will be cheaper to buy a new machine than to fix the old one.
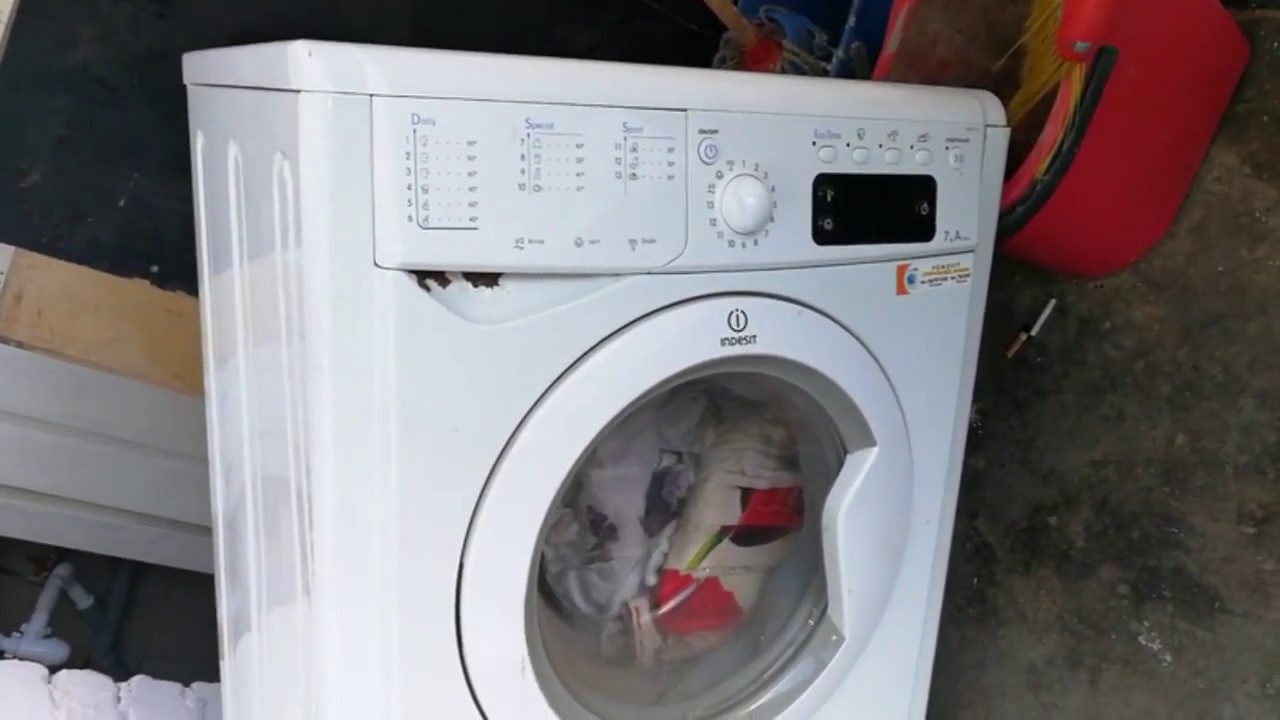
To avoid this, you can try returning the drum to its original position. This should be done carefully, using minimal effort. If it does not work out, then you should try to close the sash. This will require an elastic and strong steel wire with a diameter that fits the drum hole.
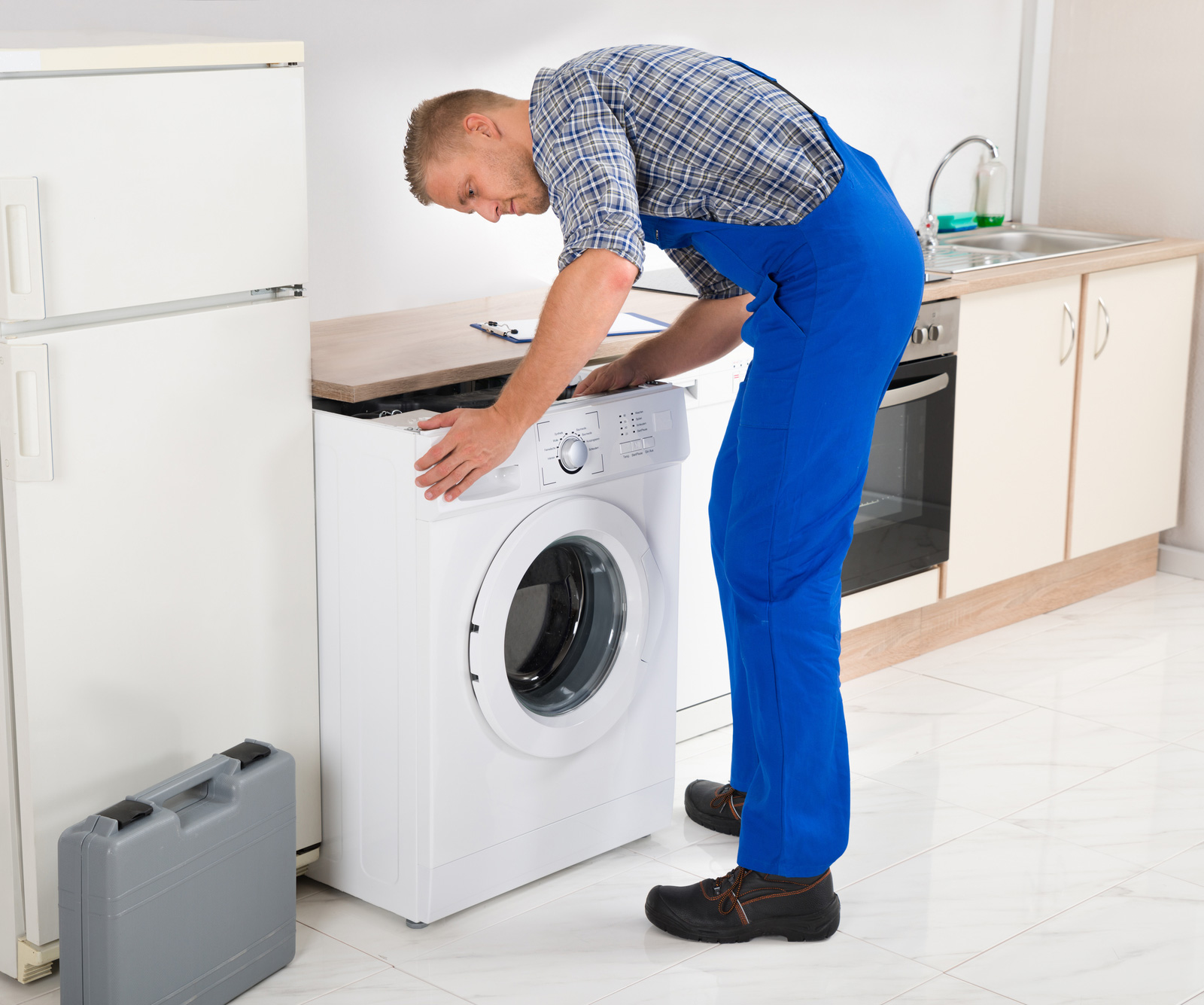
Note! If the machine has expired, you can open one of the holes in the drum a little. This will facilitate the manipulation of closing the flaps.
With the help of pliers, the end of the wire is bent in the manner of a small hook. With its help and when using a flashlight, it is necessary to try to close the flaps through the hole. If the manipulation is successful, you will be able to spin the reel. If not, or the sash cannot be held during rotation, it is necessary to disassemble the equipment.
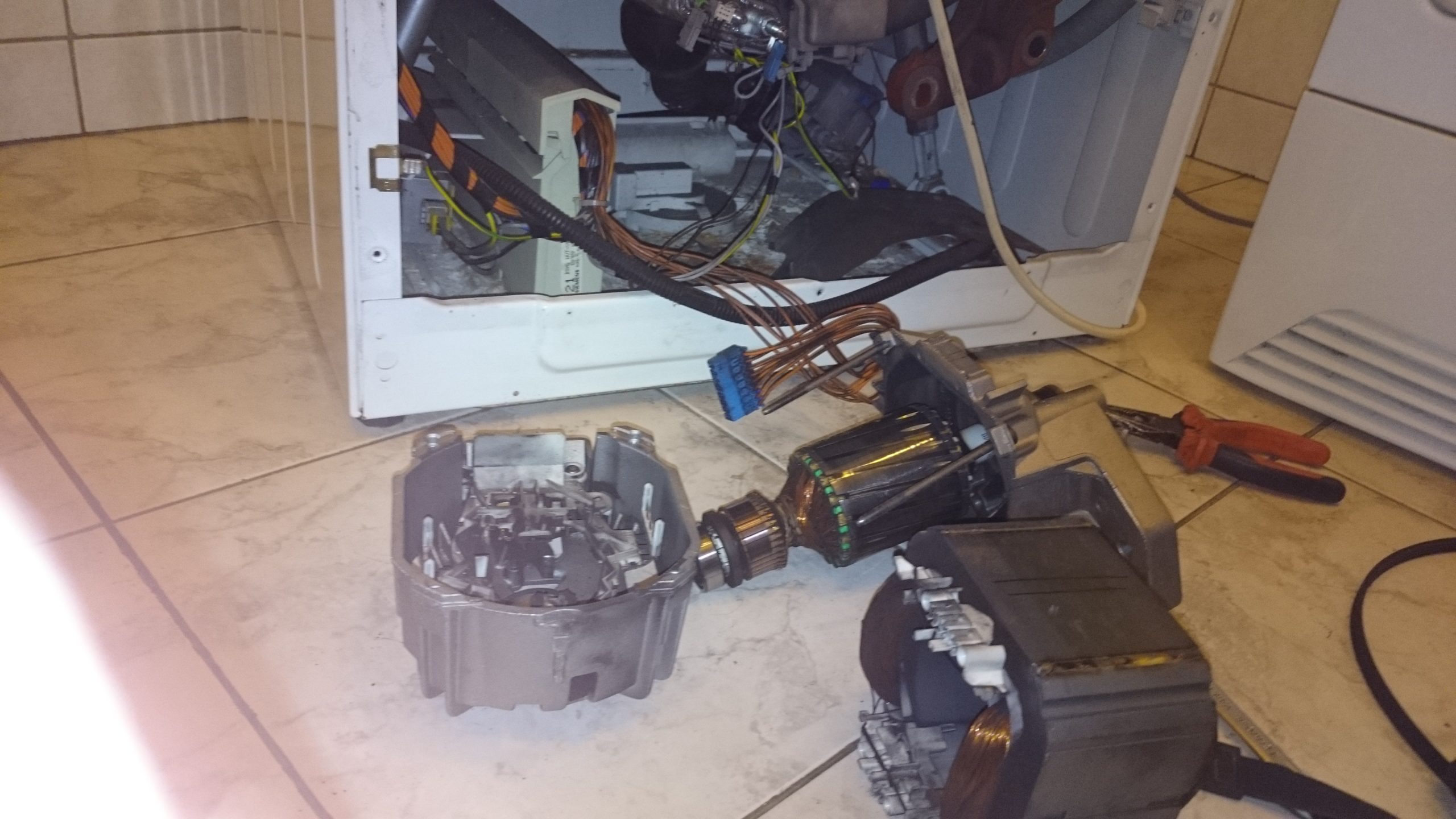
Important! When disassembling, the machine must not be laid on its side, as there is always a small amount of water in it that can get on the parts of the mechanism.
The order of work is as follows:
- Unscrew the clips on the rear panel, remove and set aside.
- Slide the side panel to the side and remove.
- Fix (remembering or photographing) the location of the wires and disconnect them.
- Unscrew the screw that holds the shaft.
- Close the loading door and remove the tank.
- Disconnect the tank halves and take out the drum.
- Clean parts from debris and dirt.
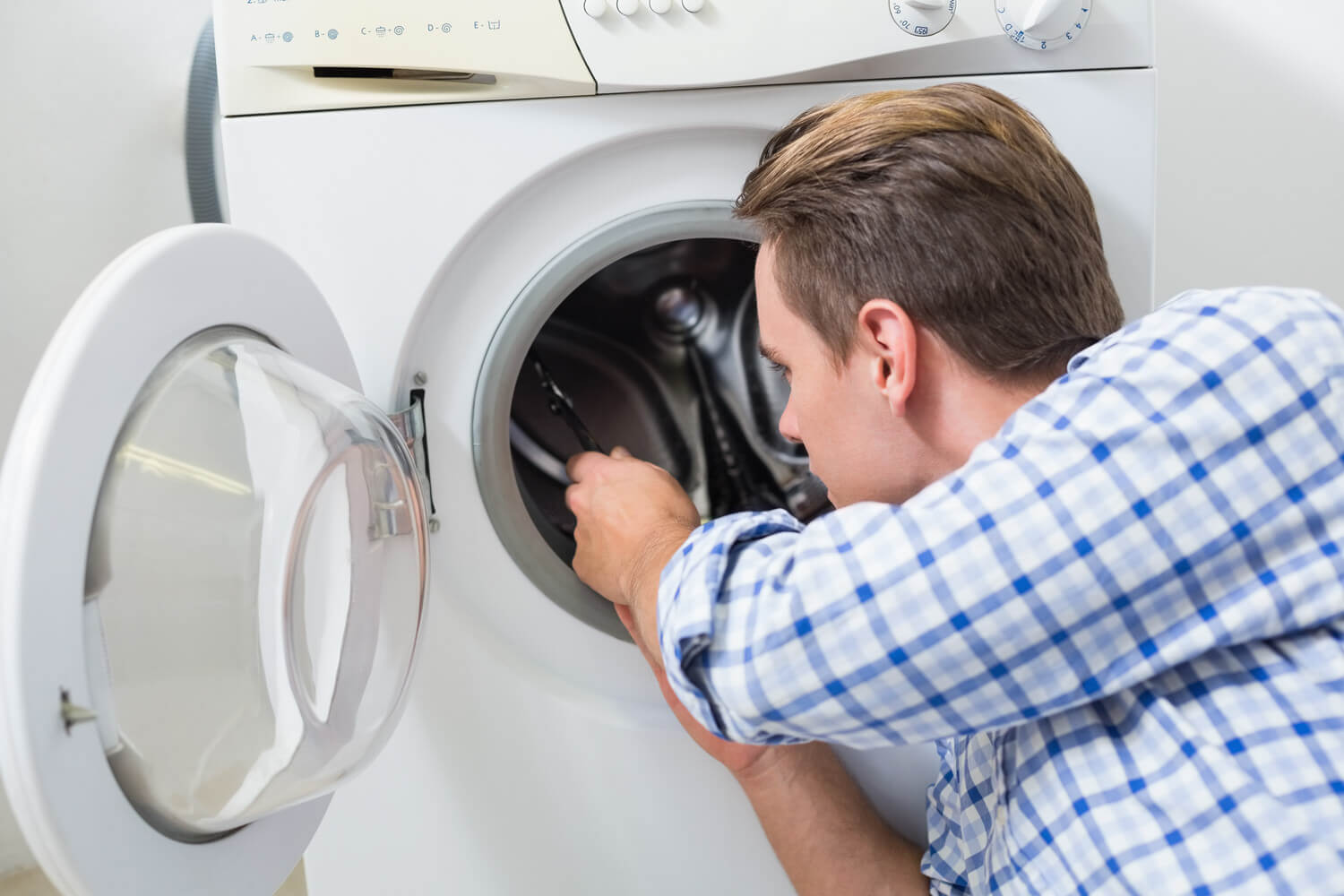
It is necessary to try to open and close the flaps several times. If the retainer breaks, it can be purchased from the manufacturer. It is also worth inspecting the damage to the heating element, flaps and tank. With significant deformations, it will be more rational to purchase new equipment.
Seized bearing
Bearing wear is a common cause of drum stalling. It must be replaced together with the oil seals, which have a service life of seven years.
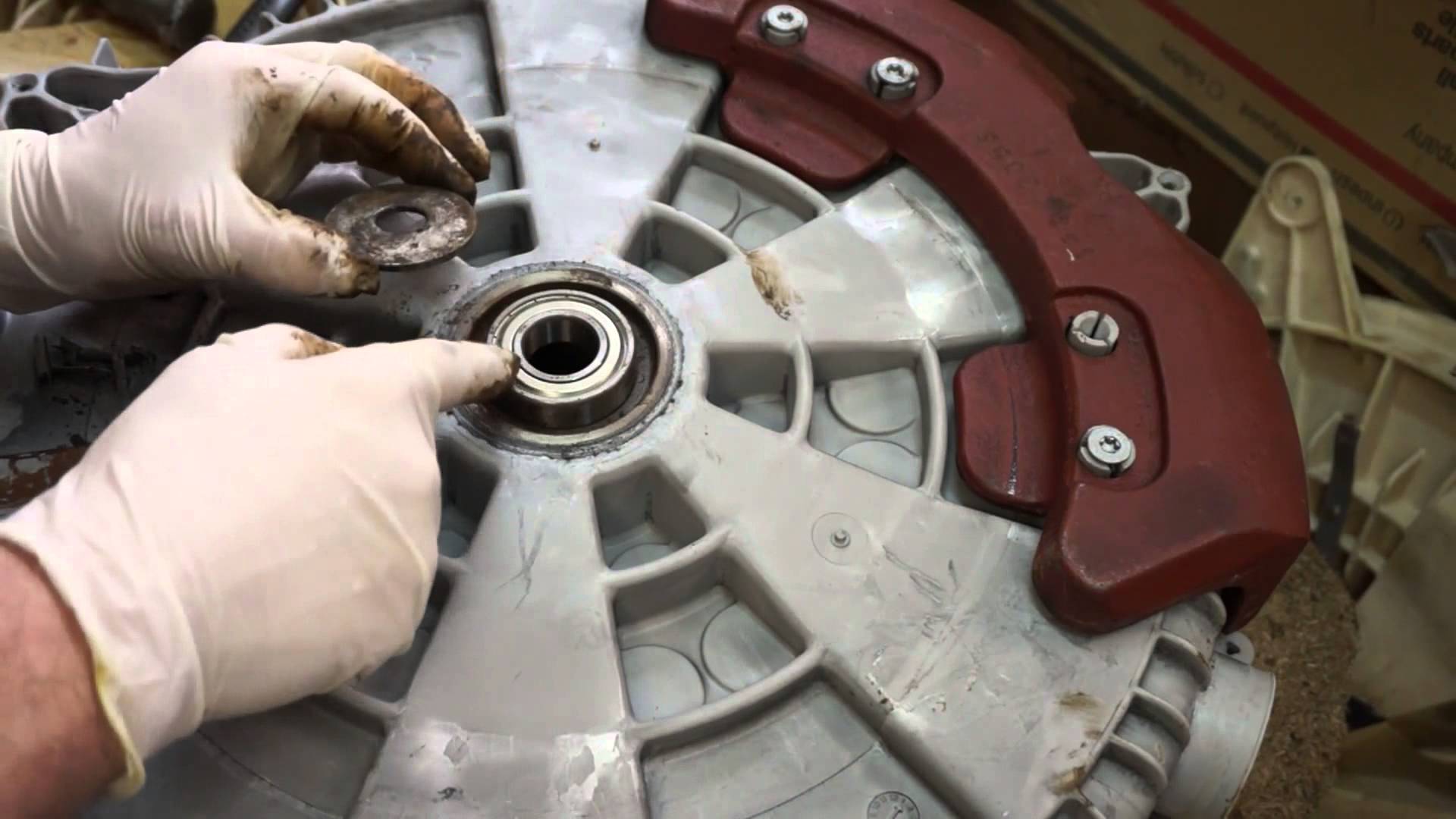
The tank must be removed to replace the bearing. It is done like this (for a machine with horizontal loading):
- Unscrew the fasteners, remove the top and rear walls.
- Dismantle the dispenser.
- Unscrew the clips on the control unit and remove it.
- Open the loading hatch, unscrew the rubber collar and insert it into the drum.
- Remove the lock, remove all fasteners and the front panel.
- Remove the counterweight with a loose clamp.
- Pull out the heating element, fixing the order of connecting the wires.
- Remove the actuator and connections.
- Unscrew and remove the engine.
- Remove the tank with a drum.
For convenience, the tank can be placed on the table. It is required to knock out the bearings from it, remove the oil seals, process the socket with lithol and install new parts, securing it with a hammer.
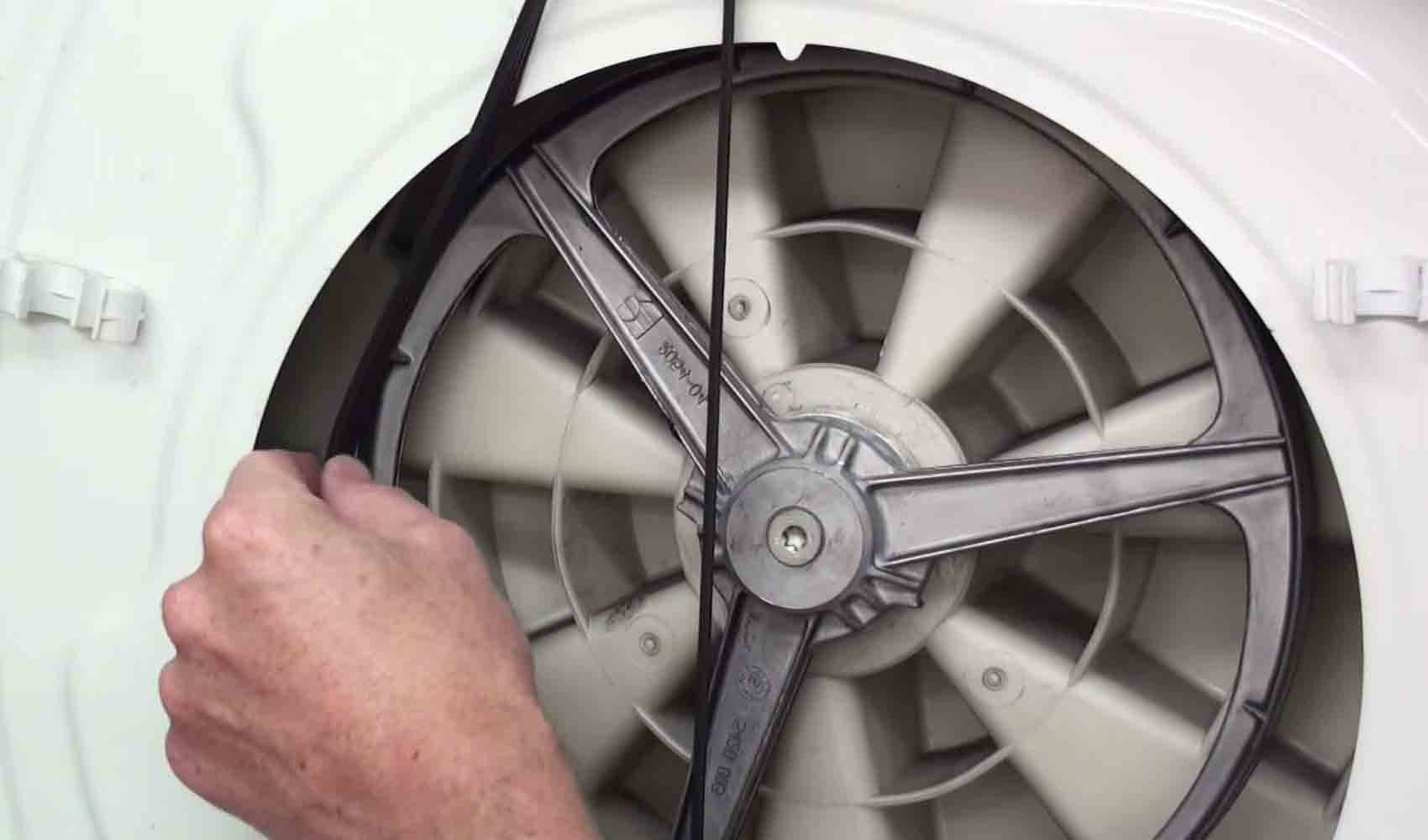
When assembling the drum, the installation must be carried out extremely carefully, treating the joints with a sealant.
Note! It is better to entrust the repair of machines with a non-separable tank to a specialist.
Drive belt problem
To assess the condition of the belt, the back cover is removed. It can slip off, and then it is enough to put it back in place. In case of damage or severe wear, replacement is required. Belts are V-belts (with an asynchronous motor) and V-belts (with a collector).
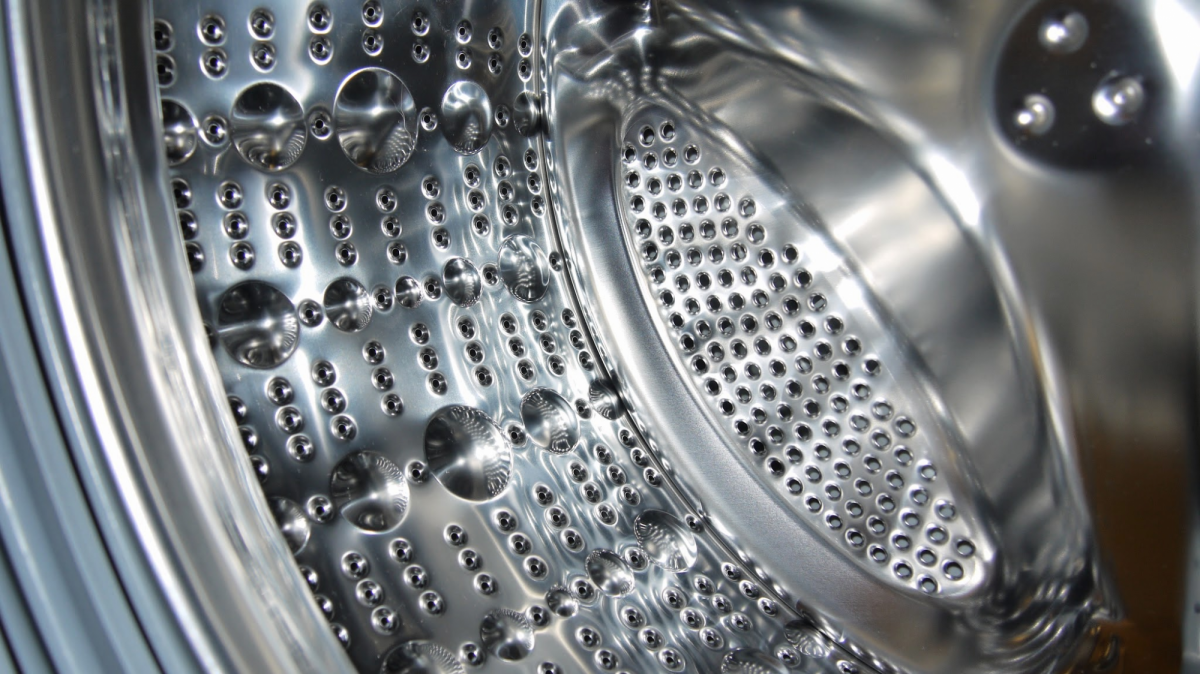
They are made of cotton material, polyester cords and chloroprene rubbers, which provide elasticity and high strength. V-belts are less tight than V-belts. To install the belt, it is wound on a pulley, completely placing it in the drum groove by rotating the pulley.
Wear of the brushes of the electric motor
Worn brushes do not produce the required electromagnetic field, which leads to the rotor stopping. In the process of use, they are shortened, and therefore need to be replaced. Their average service life is seven years.
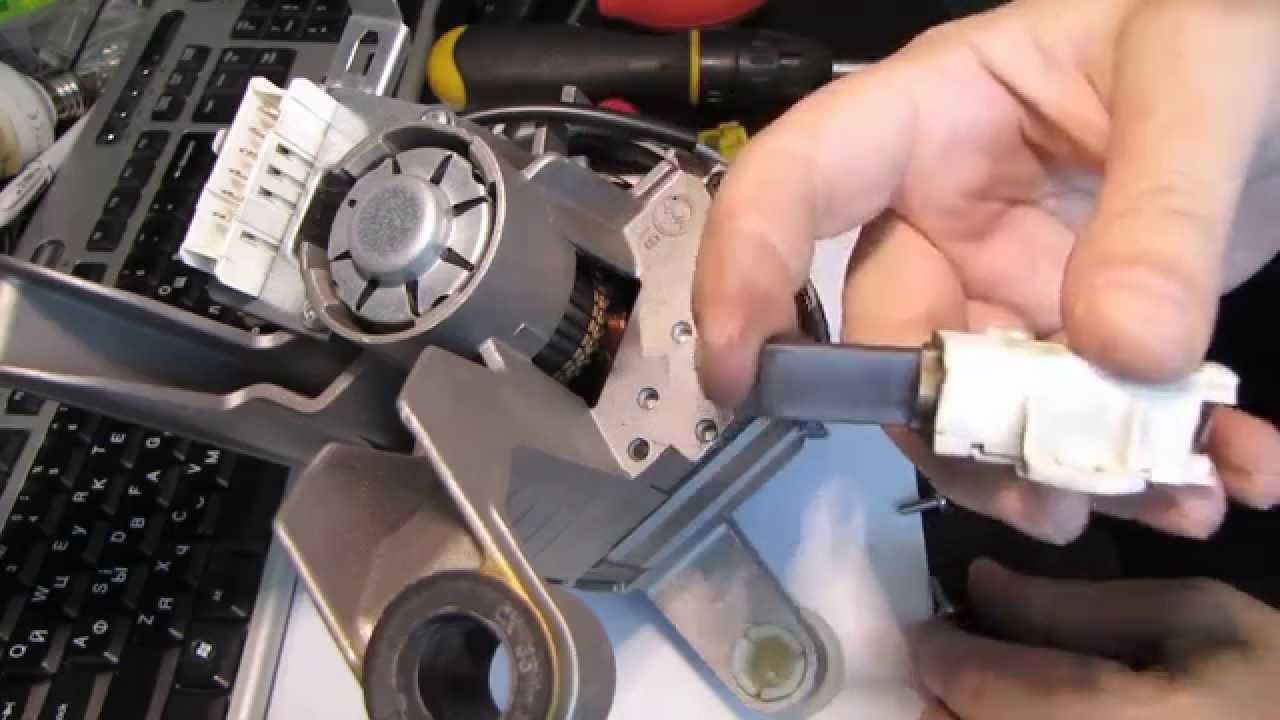
Note! It is necessary to purchase the same brushes that are suitable for this model and have no defects. When installing parts with different rigidity, the engine will fail.
Replacement of brushes is carried out as follows:
- Remove the back panel and belt.
- Disconnect the power supply to the motor by removing the connector with the wires.
- Dismantle the engine.
- Lay the motor on its side with the brush body on top.
- Unscrew the fastening bolts and remove the spare parts on both sides.
Inspect the brushes before replacing. If they are more than one and a half centimeters long, but the cause of the breakdown does not lie in them. At the same time, you should clean the collector from plaque by removing scratches with sandpaper. Then you can install new parts and fix them.
Failure of the control module
Usually, the control board breaks due to normal wear and tear or voltage drops. There are several options for action: flashing, resetting programs, or replacing the module.
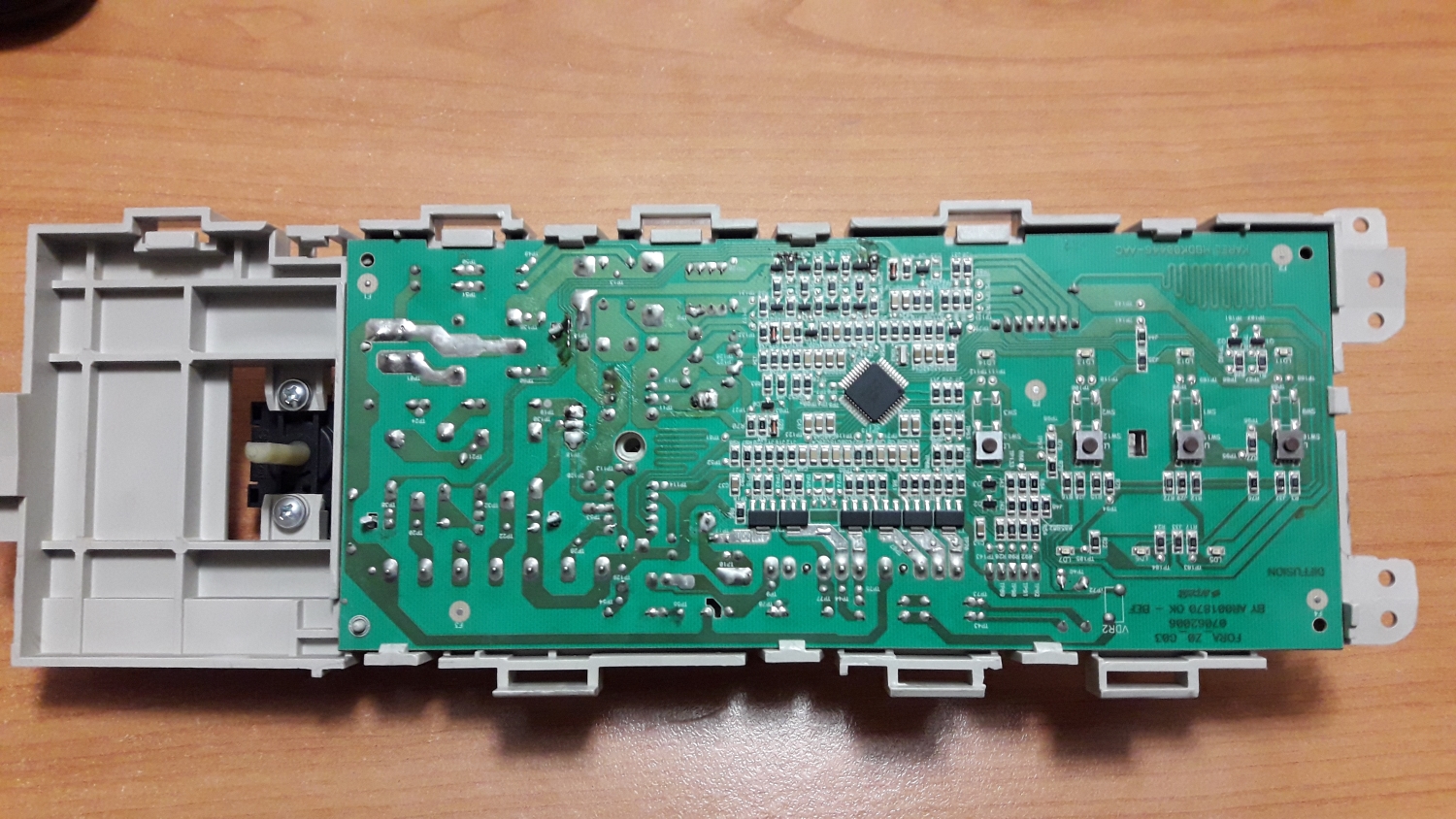
Note! Some models have a self-check feature that identifies the source of the problem.
If there is a need to remove the board, this is done by dismantling the upper part of the machine and removing the module. To repair this unit, special skills are required, and therefore it is worth removing the fee only if the warranty period expires.
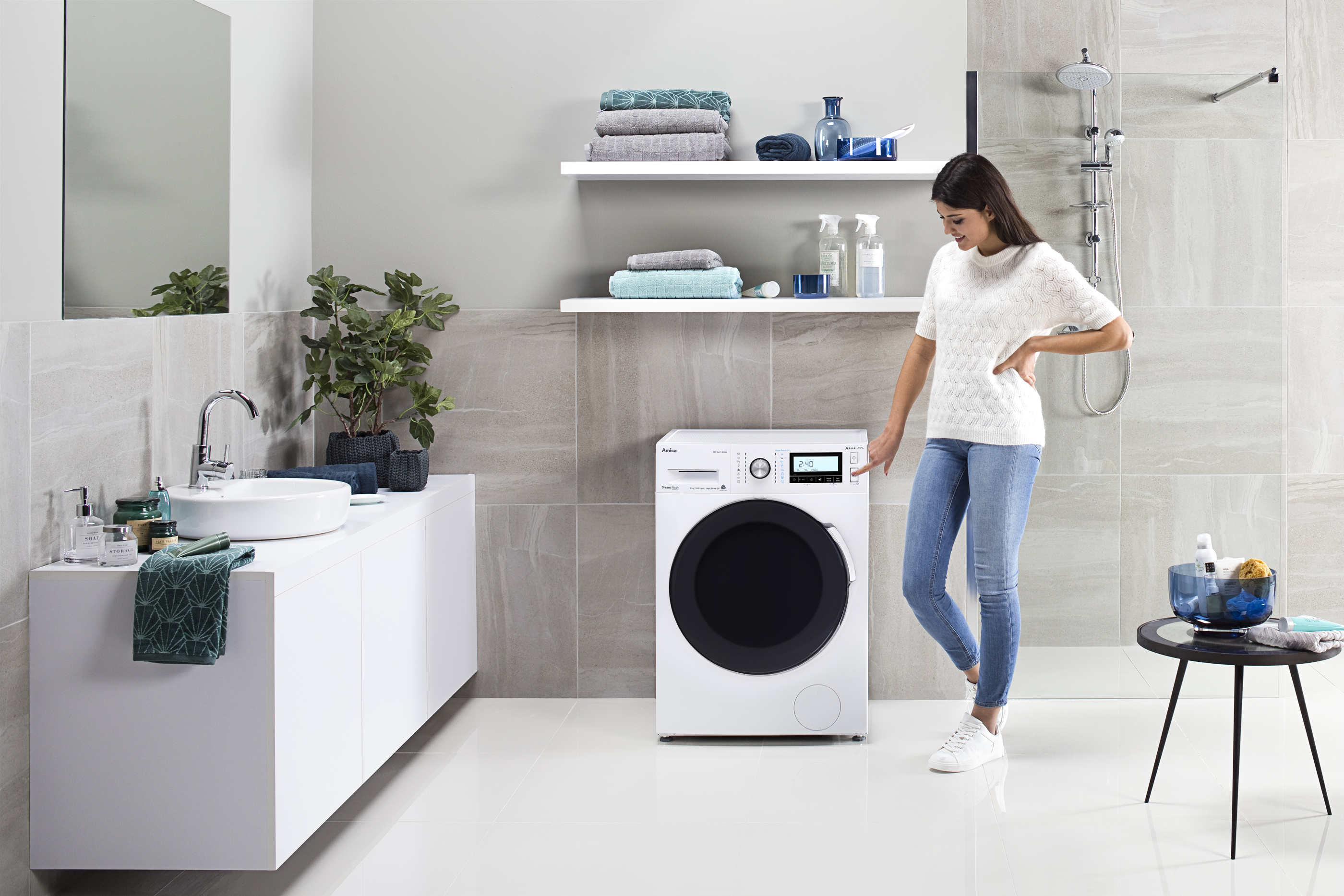
There are several signs that an intervention is needed:
- darkening of the tracks, the appearance of tan marks, discoloration in some areas;
- viewing the bulges on the caps of the capacitors;
- fading of the lacquer coating of the damping coils;
- darkening of the processor at the installation site.
The solution of these problems should be entrusted to a specialist.You can independently clean the contact groups and remove the soot layer from the power filter coils.
Engine breakdown
Usually the motor is the most reliable part of the machine, however, it can also fail if the winding near the rotor or stator is short-circuited or broken. In the first case, the empty drum spins freely, but the corks are knocked out during washing. In the second, the drum does not rotate.
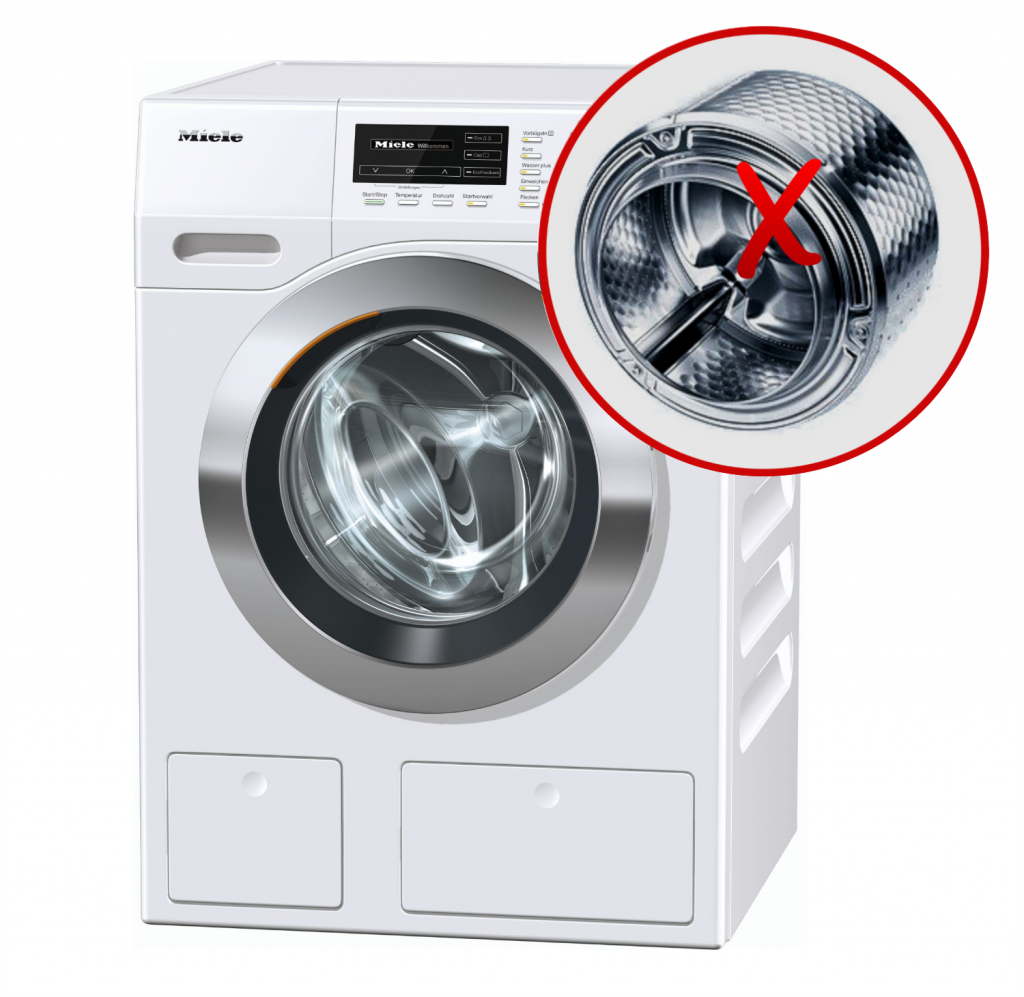
Repair is carried out in the case when the machine continues to hum when the drum stops. If the launch is not carried out, there is smoke, it smells like burning and sparks fly, then a complete replacement of the engine is necessary. The motor is removed in the same manner as for removing the belt. It is necessary to remove the retaining bolts and disconnect the power terminals. The main faults are lamellas, brushes and windings.
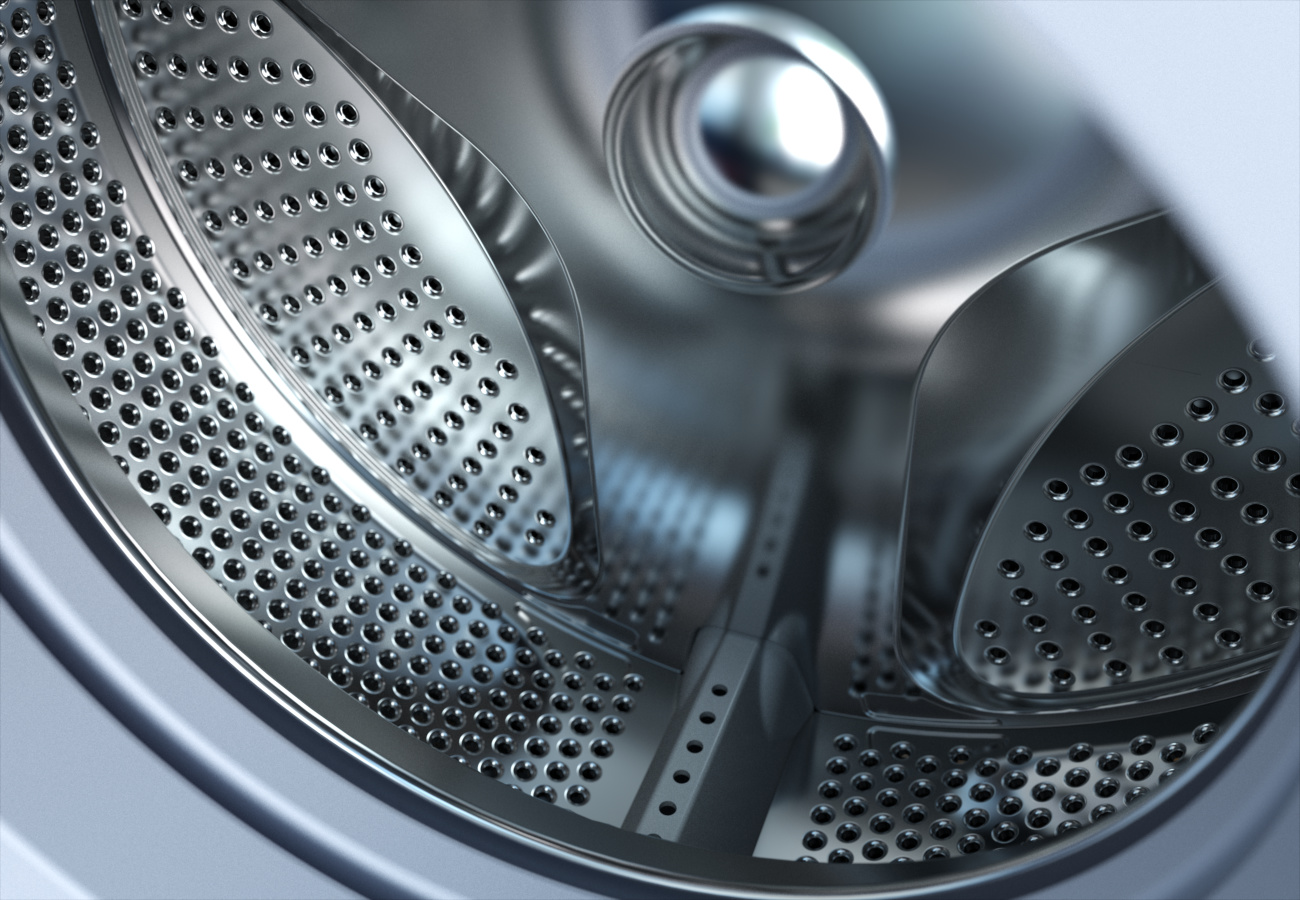
You can check the performance of the windings using a multimeter. The discrepancy should not exceed 5 ohms. Deterioration of lamellas is determined by inspection for flaking, burrs and breaks. Parts need to be replaced, not rewound.
What to do if the drum does not spin
Trouble diagnosis
You can name the following diagnostic symptoms that help determine the cause of the malfunction and how to fix it:
- The program is running, the motor is humming, but the drum in the washing machine does not rotate - changing the drive belt.
- The machine does not pick up speed during the spinning phase or does not rotate the drum, the motor sparks - replace the brushes.
- After starting, the machine locks the door and starts collecting water, but the drum does not rotate - diagnostics and repair of the control unit or replacement of the engine.
- The machine does not wring out or rotate the drum - replacement of the tacho sensor that controls the rotation speed.
- First, the machine rattles during spinning and does not spin, and then the drum stops spinning - replacing the bearings.
- The motor does not hum and the drum does not rotate - restoration of wiring or contacts.
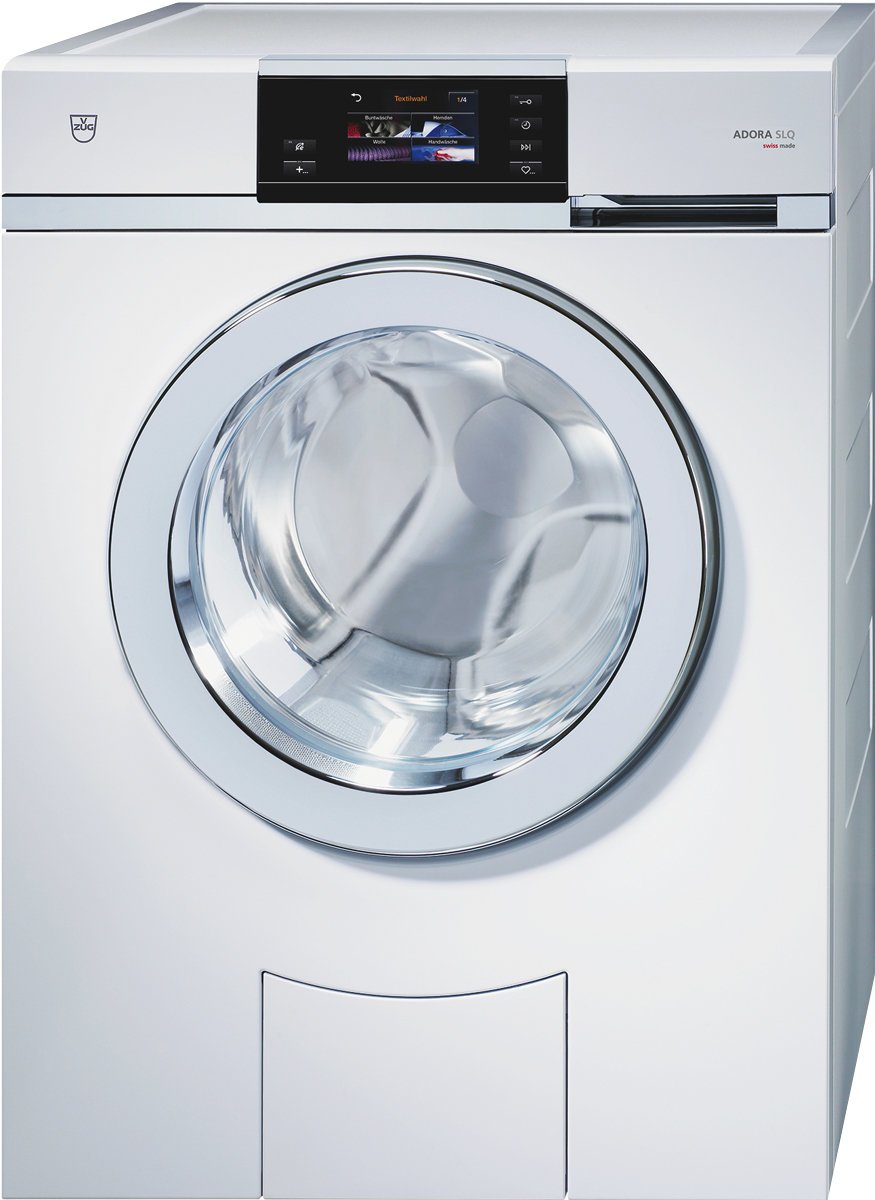
Self-repair and replacement of parts
It is quite possible to independently determine the malfunction of the machine, but for this you need to have certain skills. In the absence of experience with technology, it is not worth replacing parts, as this can lead to an aggravation of the breakdown and deterioration of the general situation.
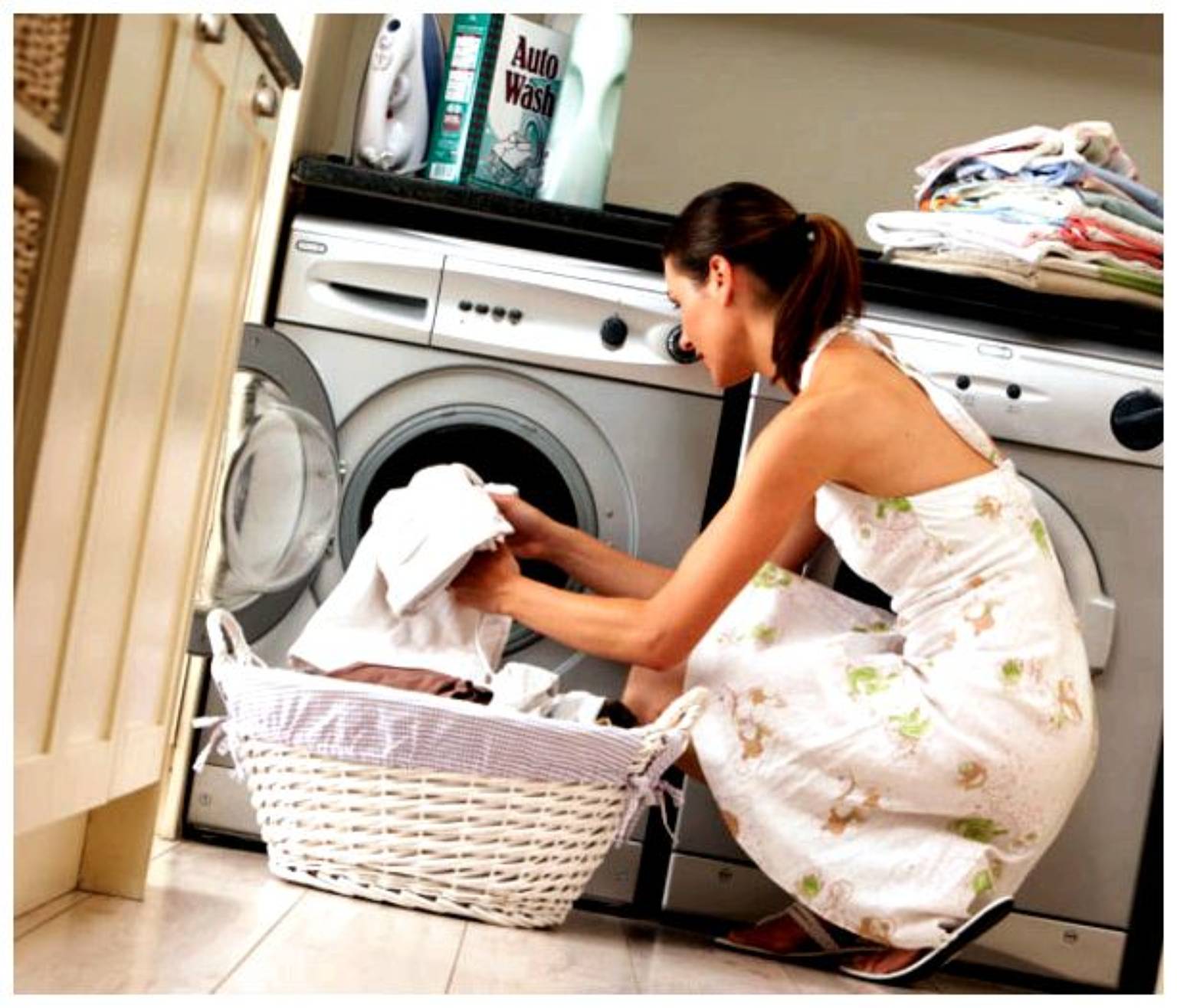
Problem prevention
The following methods are recommended to prevent future problems:
- Check pockets of clothing carefully before washing.
- Wash underwear, socks and handkerchiefs in special bags.
- Do not overfill the tank, observing the manufacturer's recommendations for maximum loading.
- Distribute items evenly over the drum.
- Connect the machine through an extension cord that blocks the drops, or an uninterruptible power supply. Especially important with frequent power surges. It is also necessary to correctly ground the machine during installation.
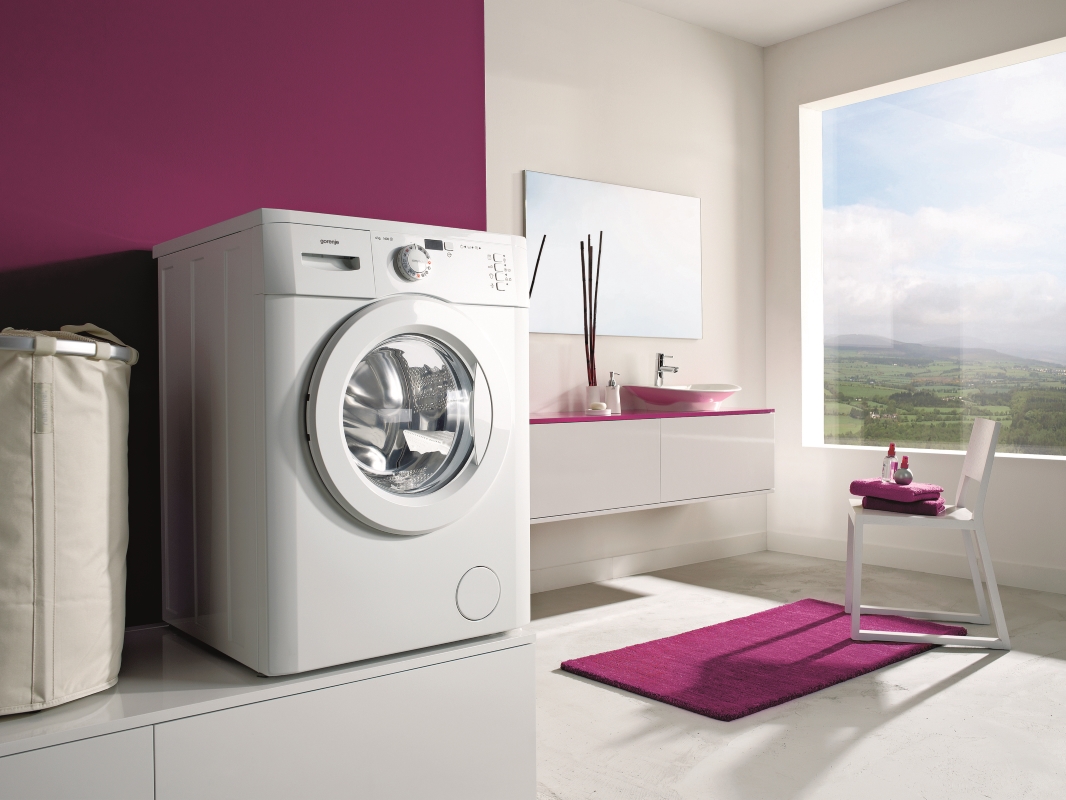
General washing machine care rules
After washing, do the following:
- let the loading door and powder containers dry;
- remove small objects and debris from the drum;
- rinse the powder container to avoid the appearance of mold;
- clean the rubber gasket and wipe dry.
The clipper should be cleaned regularly by running one dry cycle using a mixture of powder and bleach.
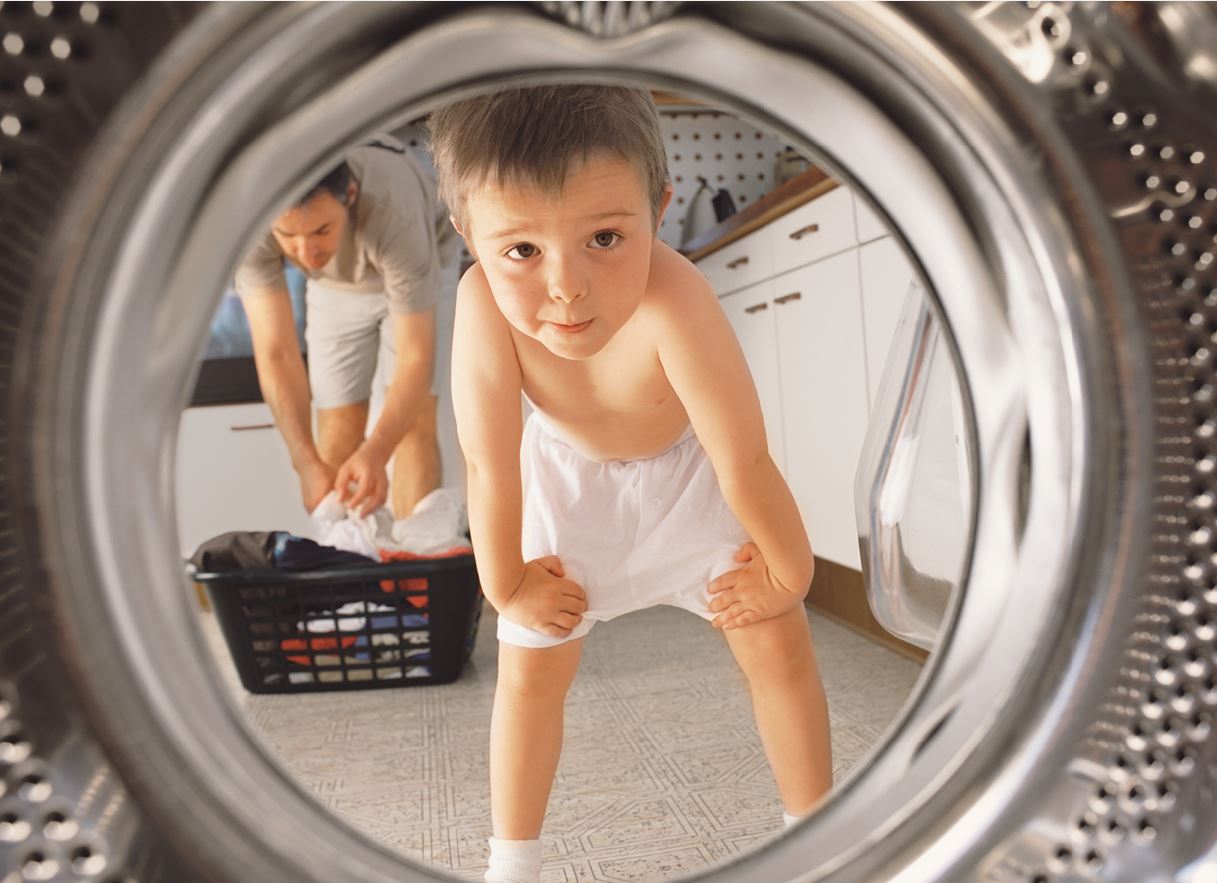
There are many cases when the washing machine is running, but the drum is not spinning, and each problem needs a special approach. Competent operation of equipment will avoid or delay the appearance of any malfunctions.
Video: all the reasons why the machine does not spin the drum